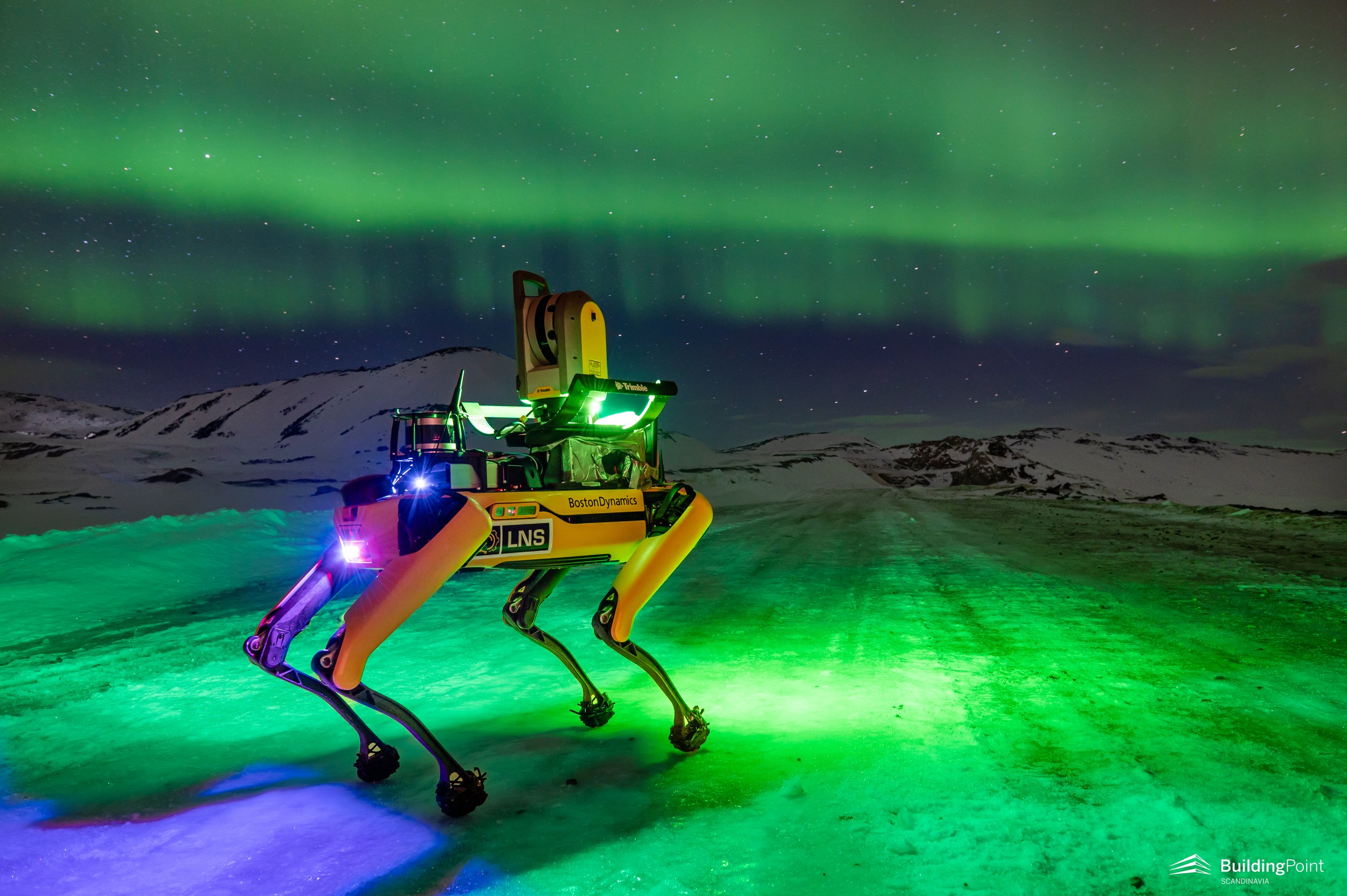
Spot
Unleash your productivity with a clear and continuous picture of progress on your job site with Spot - the Autonomous Construction Robotics Solution.
What is Spot?
If you combine an autonomous robot, BIM, satellite navigation, laser scanning and artificial intelligence, what do you get? You get a safer and more productive workplace!
Unsafe environments, risks in the work environment or huge areas can make it difficult for us humans to perform certain jobs. And that's where Spot comes into the picture.
Trimble has launched a system by combining Spot from Boston Dynamics with its Trimble X7 laser scanner. The system is controlled via Trimble's FieldLink software, which enables real-time data in both the workplace and the office.
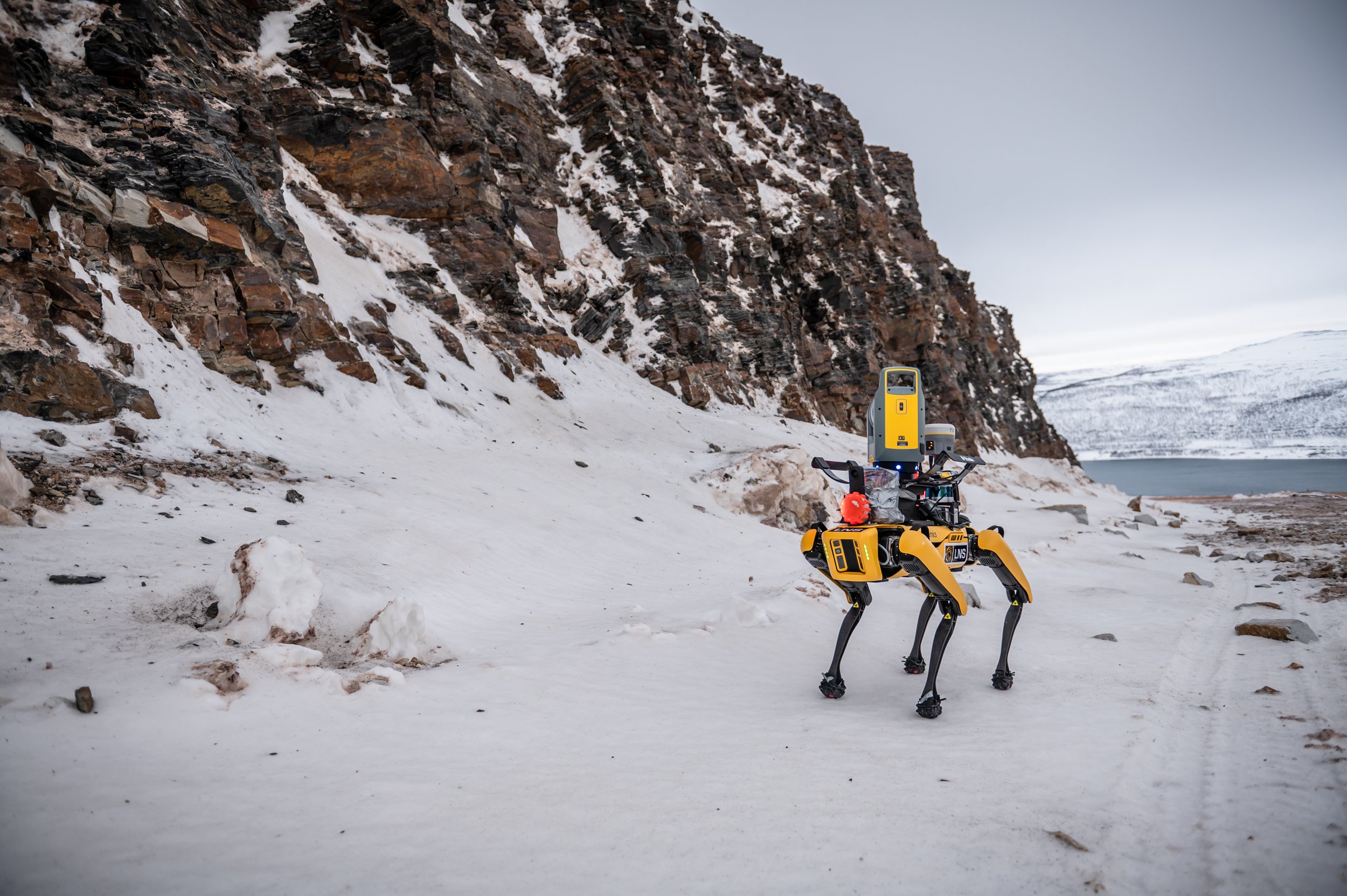
See how LNS use Spot in arctic mining
Autonomous or remote controlled
Spot can be controlled in two different ways; It can be controlled remotely by an operator, or as a completely autonomous "intelligent" robot that performs the tasks you have pre-programmed.
Autonomous Control
With autonomous control, you need to train the robot for the tasks to be performed. You guide Spot through the mission and define waypoints. Spot maps the environment on site during training and each waypoint is defined as a unique mission.
When the training is complete and the mission is defined, Spot will collect data / point clouds at each unique waypoint. With autonomous control, no operator is needed. Spot can perform the same mission in exactly the same way at the exact same time - every time.
A big advantage of this solution is the possibility to get "as-built" scan data in real time from the construction site!
Remote control
When you control Spot remotely, you see through Spot’s “eyes”. With support from Spot’s other sensors you can easily navigate Spot around the site, or you can initiate a program and let Spot do the job autnonomously while you do other things.
Controlled by an operator locally
Spot can be of course also be controlled by an operator on-site. The operator can then put spot to work there and then, e.g., at a site where access to the area that shall be scanned is dangerous for people. Or one can program spot for future operations when the operator is not on-site.
VIDEO: Teaser trailer for the video report from LNS field trials. Watch the full length video here (9 minutes long)
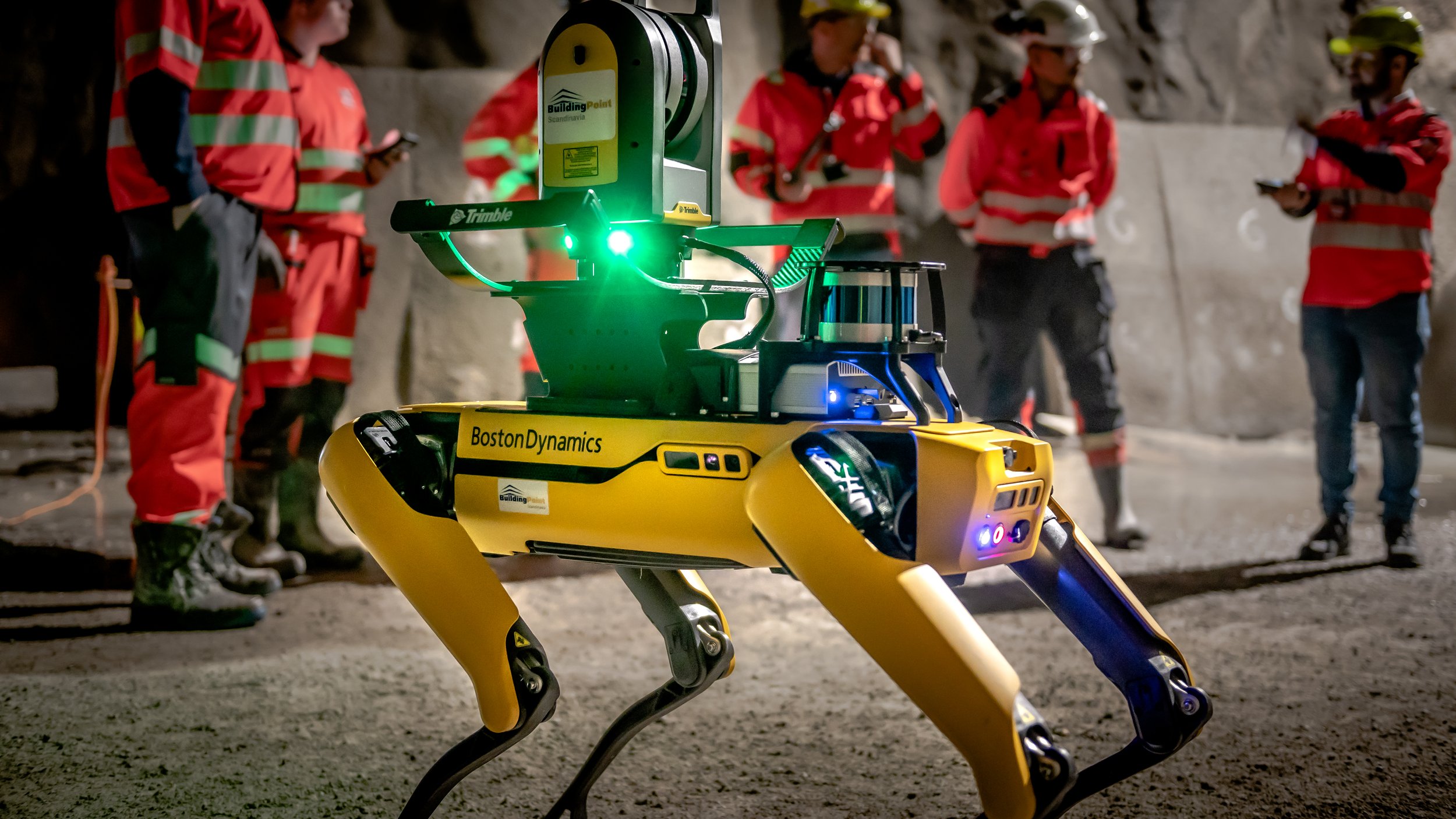
Spot makes Tunnel Scanning safer and more efficient for Veidekke
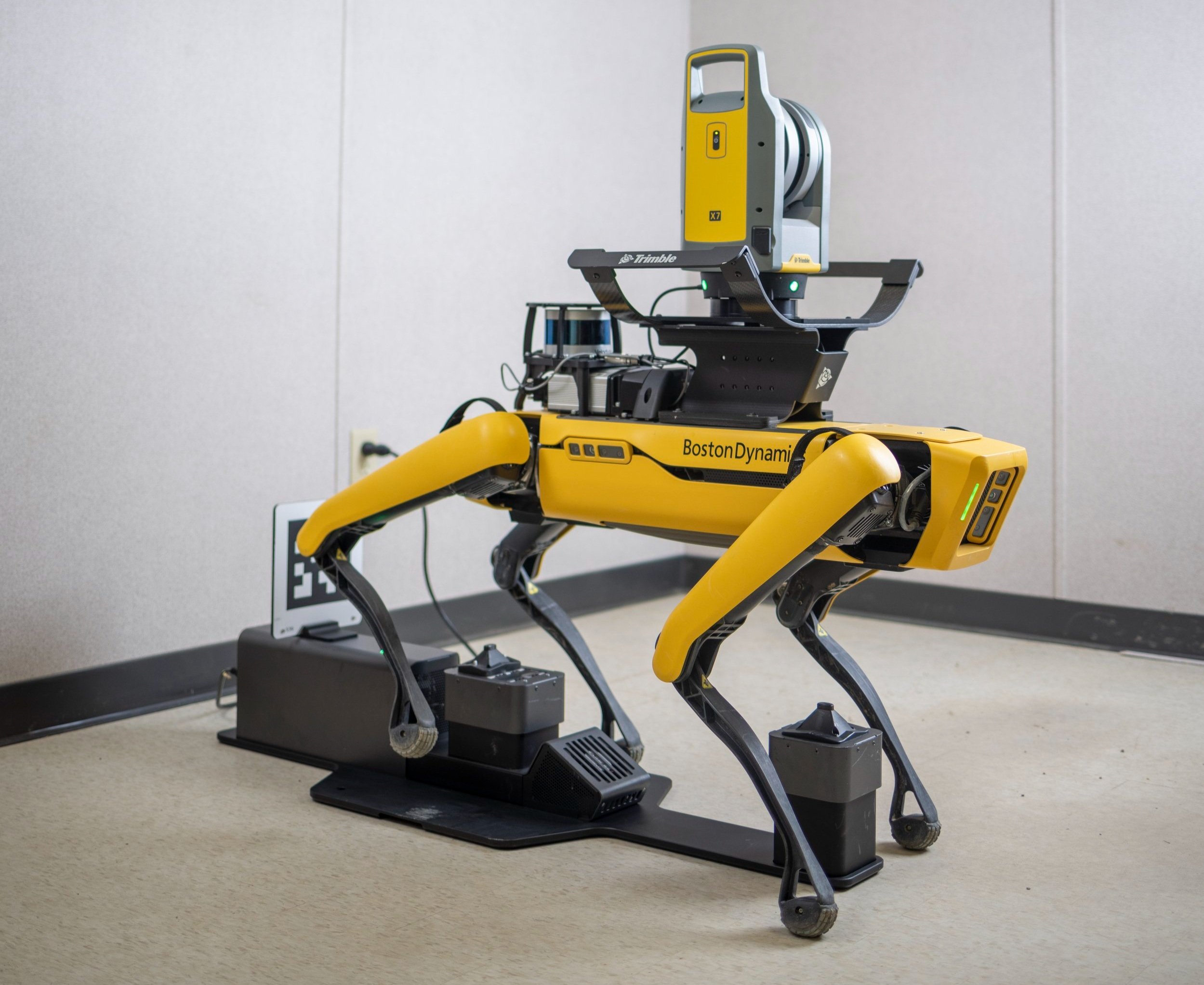
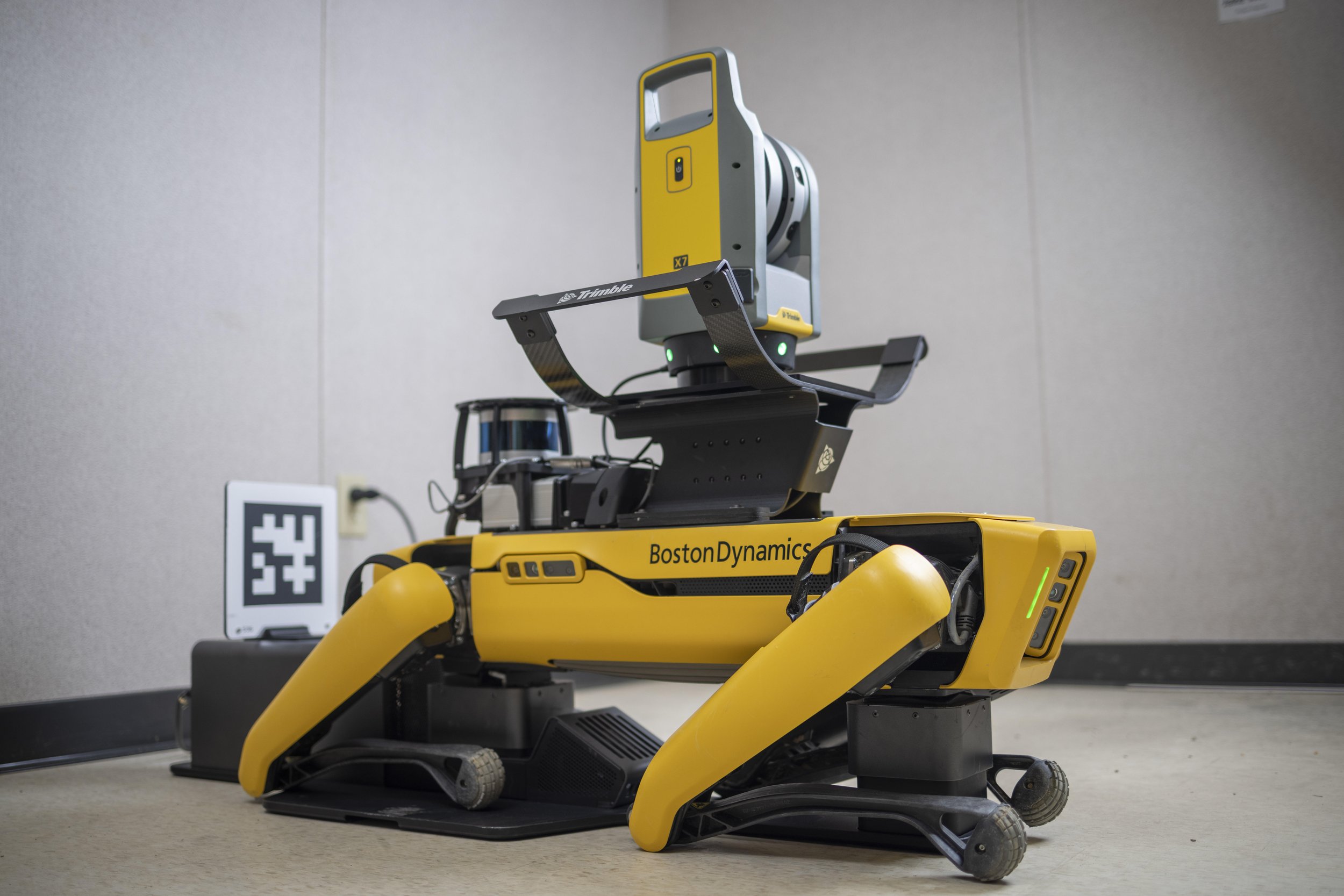

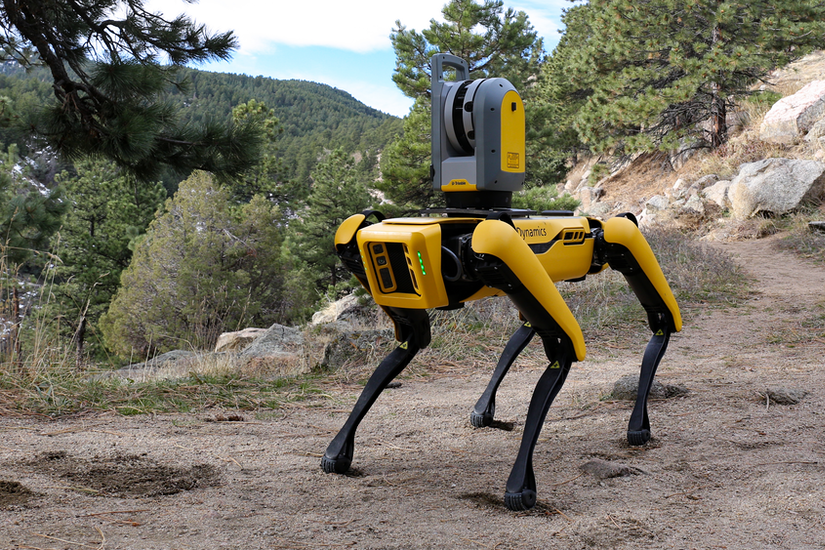
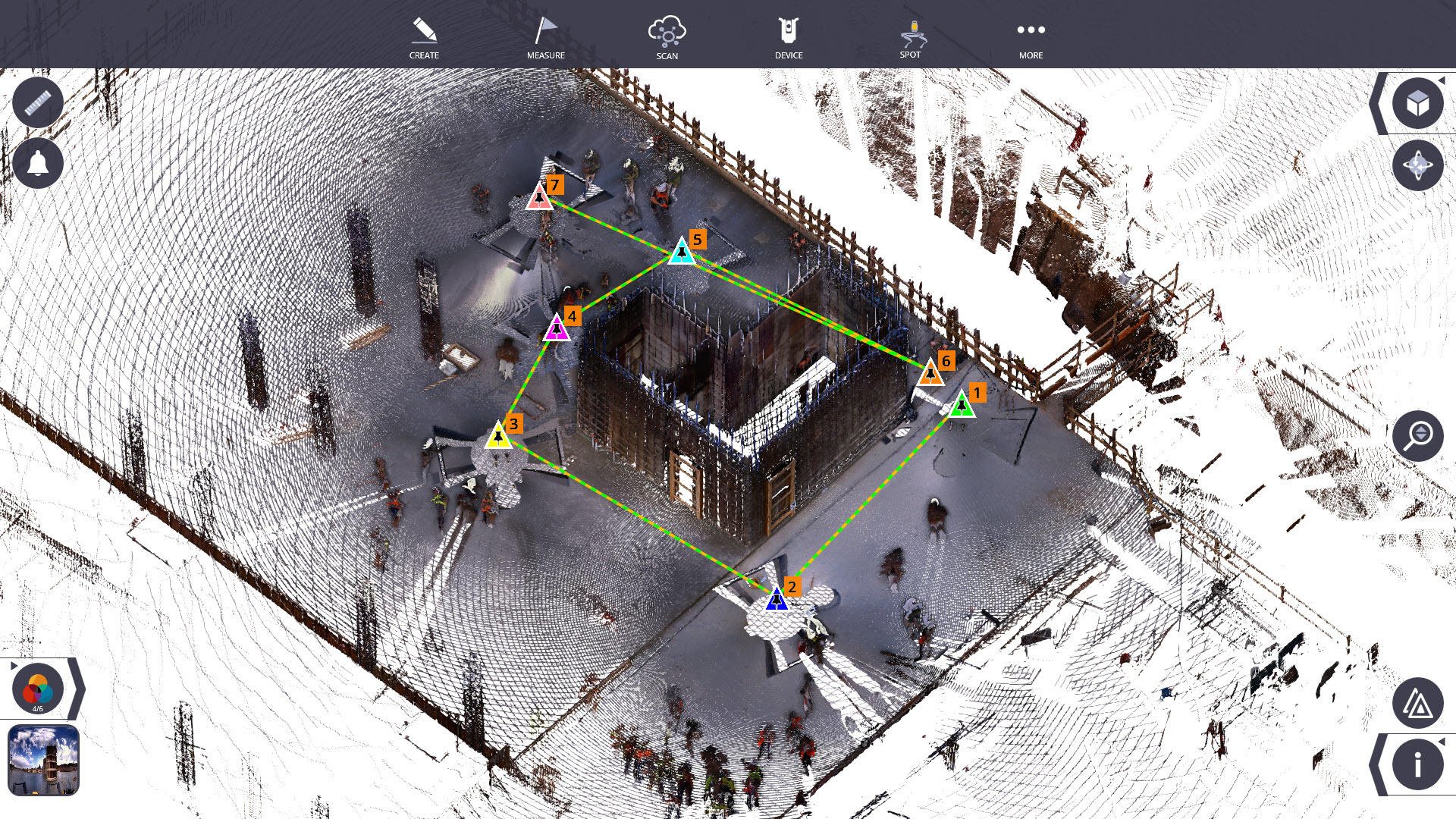
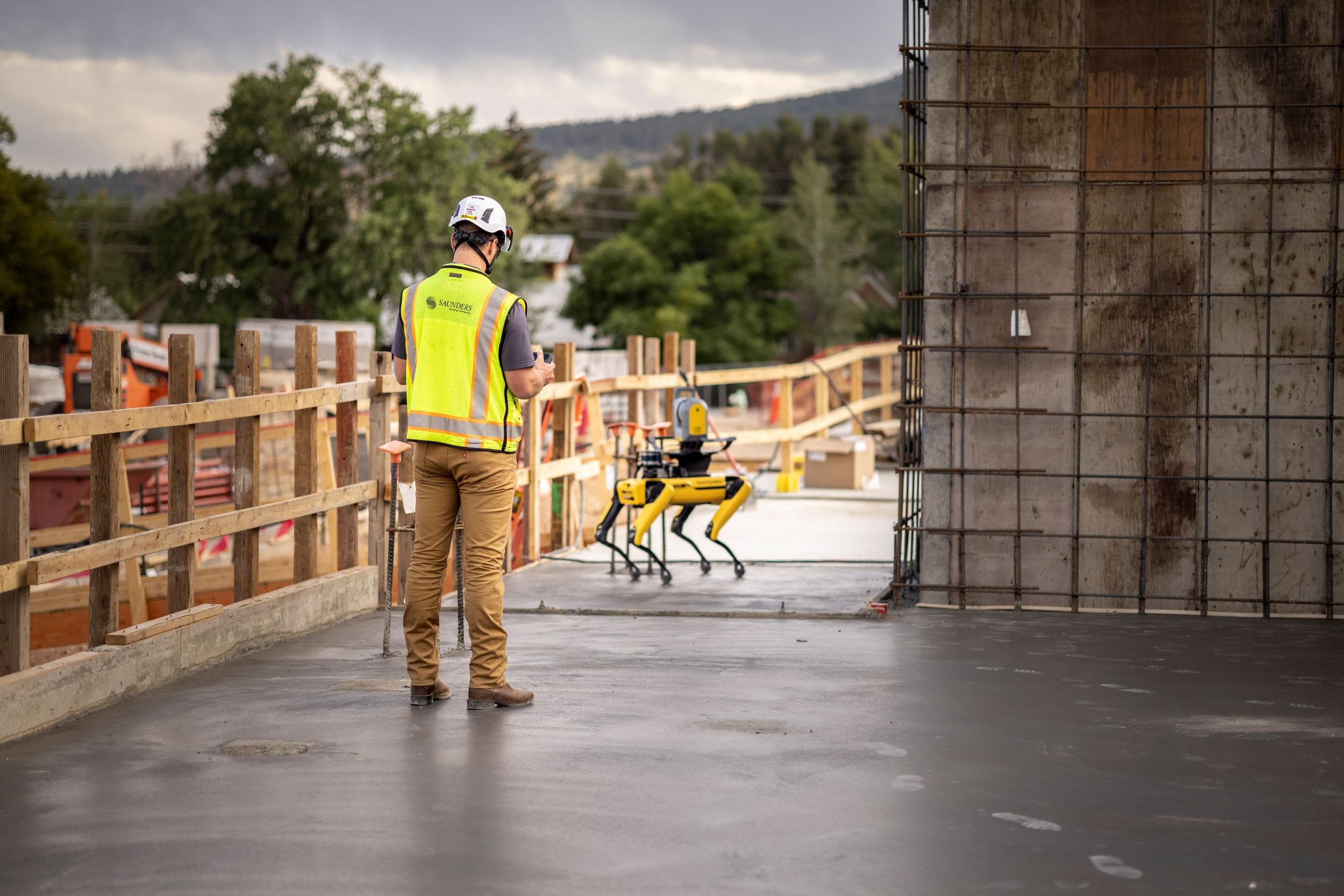
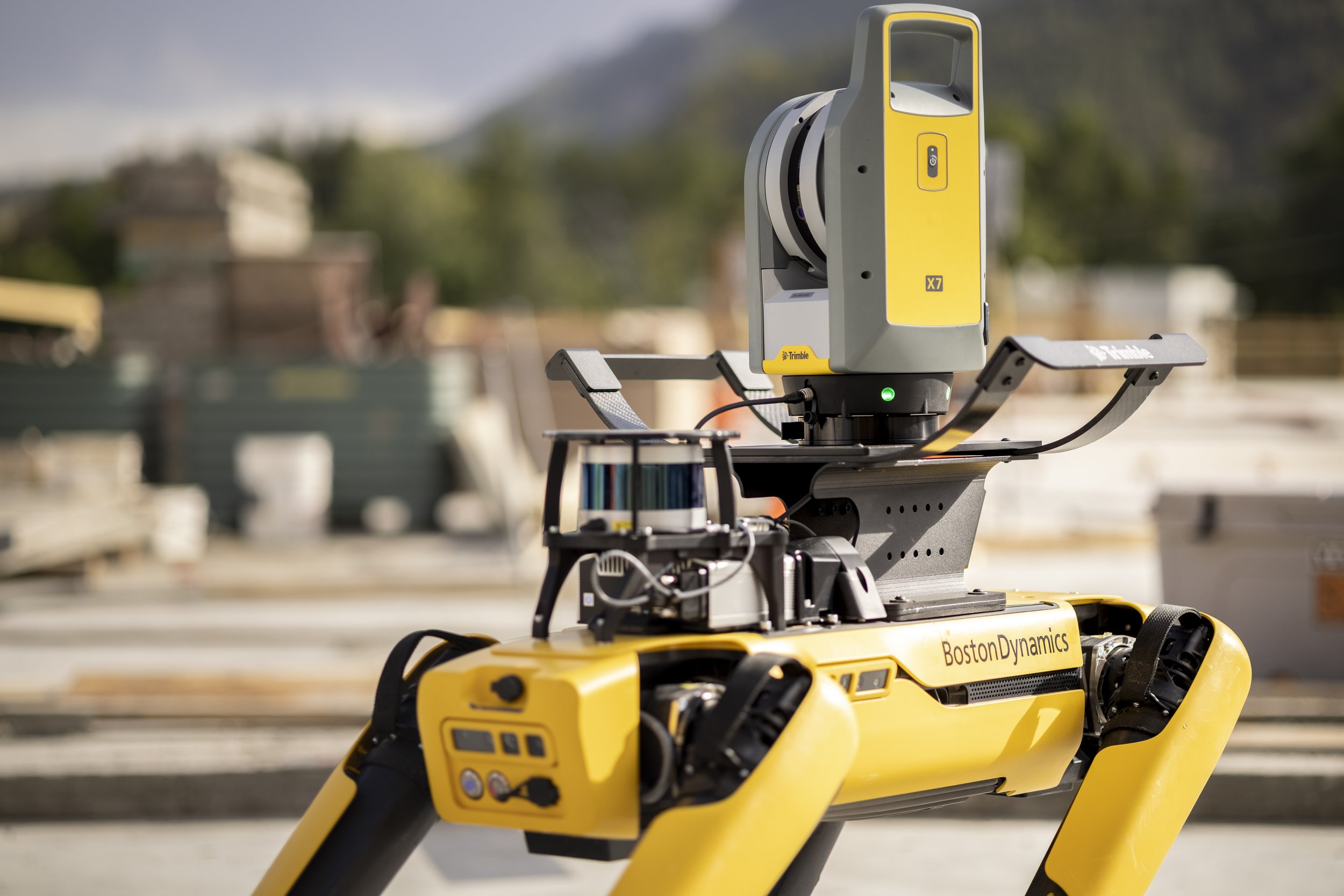
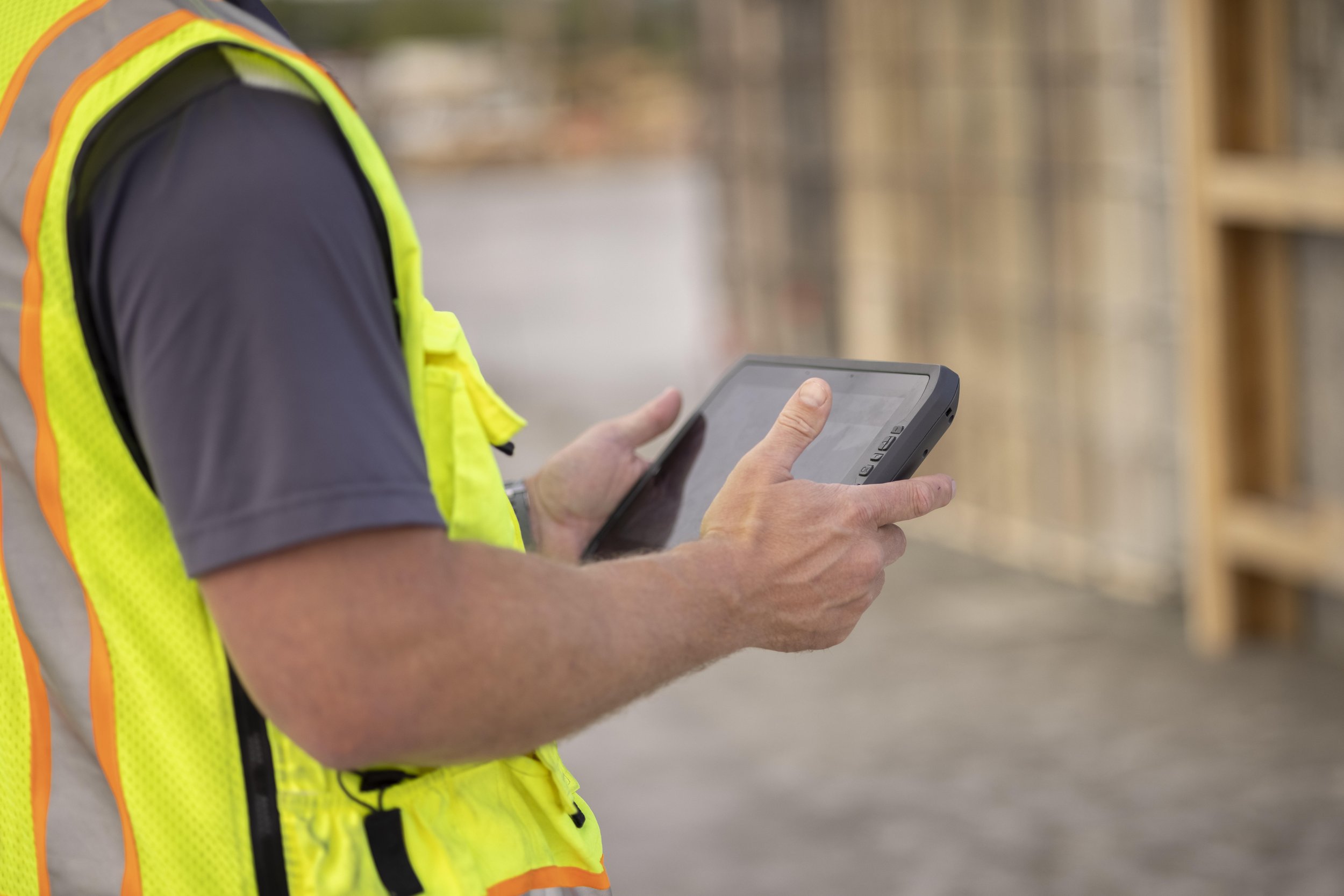
Collect Point Clouds with the Trimble X7
Point clouds collected with the Trimble X7 scanner can be geo-referenced directly to the workplace coordinate system or just as individual layouts.
For remotely controlled assignments, the data is collected and automatically made into a composite point cloud directly in FieldLink before Spot leaves the workplace.
With the autonomous control, the point cloud is sent to the office when Spot has docked with its charging station. Once there, the batteries in both Spot and the laser scanner are also charged so that they are prepared for the next assignment.
And of course… The Trimble X7 is GREAT on its own as well!
Features summary
Autonomous Scanning Operation
Enable the collection of consistent and reliable data for improved production and quality control monitoring with Spot the robot. Document change and perform design validation to ensure the as-built condition matches the as-designed intent.
Safe Scanning, Continuously
Send the Spot robot and the X7 laser scanner into unsafe conditions to perform dirty, dull, or dangerous tasks. Improve job site safety and address labor shortages.
Automated Scan Registration in the Field
In-field registration with Trimble FieldLink software ensures the right data is captured the first time. Perform real-time design validation workflows such as scan-to-model comparisons and surface analysis inspections to make immediate decisions in the field without leaving the job site.
Integrated Docking Station
A self-charging station for Spot transforms the robot into a truly autonomous remote inspection tool. Utilize multiple docks to facilitate long missions on remote sites. With built-in dock detection, Spot will automatically recognize where to dock to charge Spot and the X7 laser scanner.
Scan Data Upload
A built-in Gigabit Ethernet connection in the docking station enables the fast offload of registered scan data from the X7 laser scanner. Immediately access scan data at the end of a mission or post to a cloud sharing platform to perform design validation analysis.
Integrated Ruggedized Tablet
A ruggedized Trimble tablet allows you to control Spot and the X7 laser scanner through one device. Use the tablet to define a mission for Spot, set scanning parameters for the X7, perform in-field registration, design validation, and access Trimble Connect for project communication and collaboration tools.
DATASHEET:
Autonomous Construction Data Collection
With integrated Trimble solutions for 3D laser scanning, robotic total stations, and GNSS technologies for the building construction and civil construction markets.
Benefits
Scan in environments that are dangerous to humans, like mines, accident sites, areas with explosives or other hazards.
Autonomoues scanning at work at night when no one is present, avoid interruption on the construction site.
Remote scanning and operation, avoid travel-